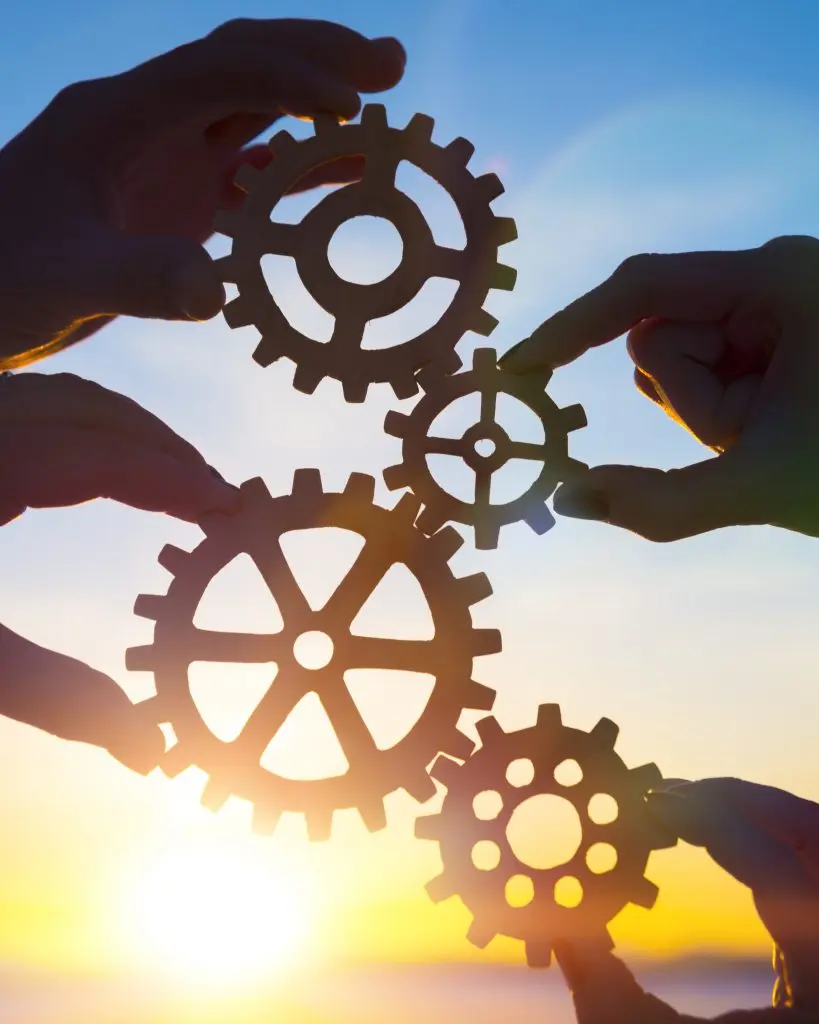
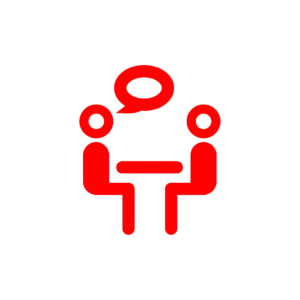
Sizi Dikkatle Dinleyelim
Sizi dinliyor ve işletmenize özel çözümler sunmak için her adımda yanınızda oluyoruz.
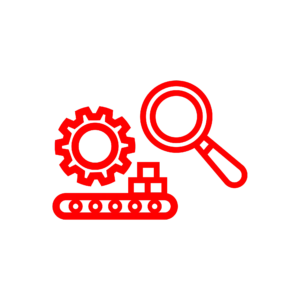
Uygulamanızı Yerinde Görelim
Süreçlerinizi yerinde inceleyerek, işletmenize nasıl değer katabileceğimizi birlikte keşfedelim.
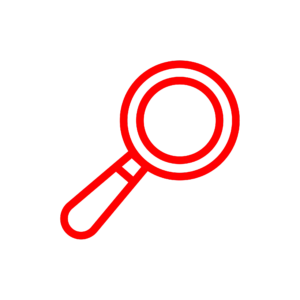
Sorunları Tespit Edelim
Uzman ekibimizle, süreçlerinizi analiz ederek olası sorunları hızla tespit ediyoruz.
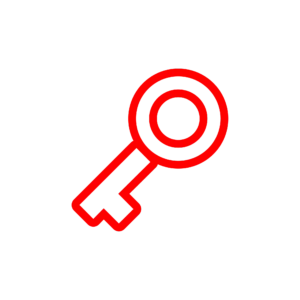
En Uygun Çözümü Sunalım
İşletmenize özel, sürdürülebilir ve maliyet etkin sistemlerle süreçlerinizi optimize ediyoruz.