Uygulama Çözümleri
Kalınlık
Kalınlık Ölçüm Sistemleri Arayanlara Yönelik
Kalınlığı ölçmenin en iyi yolunu ararken, hedefin şekli ve malzemesi de dahil olmak üzere ölçüm sisteminin türünü de kapsayan ve dikkat edilmesi gereken pek çok önemli faktör vardır. İhtiyaçlarınızı tam olarak karşılamayan ekipmanın seçilmesi, üretim sırasında hassasiyetin düşmesine ve çalışma saatlerinin artmasına neden olabilir. Bu nedenle, doğru ekipmanın seçilmesi oldukça önemli bir konudur. Dolayısıyla bu site, ölçümü güvenilir bir şekilde gerçekleştirebilmenin en iyi yolunu keşfetmelerine yardımcı olabilmek için kalınlık ölçüm sistemi arayanlara yönelik hazırlanmıştır.
İdeal ölçüm sistemini seçebilmek için bilinmesi gereken ölçüm ve ipuçları hakkında her şeyi içeren ve mutlaka okunması gereken bir kılavuz!
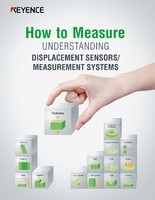
Kalınlık Ölçümü (Levha/tabaka halinde)
“Kalınlık (levha/tabaka halinde)” ölçmek için en uygun yöntemi ve en uygun ekipmanı bulabilmek için aşağıdaki örneklere bakınız.
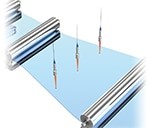
Şeffaf hedeflerin rulolar arasında ölçülmesi
Uygulama örneği: Şeffaf filmlerin kalınlık ölçümleri
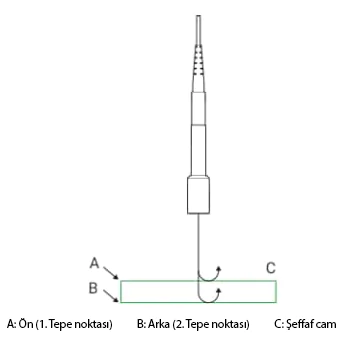
Önemli noktalar
Yer değiştirme (deplasman) algılayıcılarının seçimi önemlidir
• Yer değiştirme (deplasman) algılayıcıları üst ve alt yüzeylerin her ikisini de görebilmek için yeterli aralığa sahip midir?
• Üst ve alt yüzeylerin yansıması farklı olsa bile düzgün ve tutarlı ölçüm gerçekleştirmenin mümkün olup olmadığını kontrol ediniz.
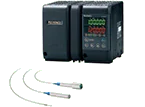
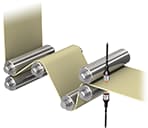
Opak hedeflerin rulolar arasında ölçülmesi
Uygulama örneği: Plastik levhaların kalınlık ölçümleri
Kalınlık, hedefin iki algılayıcı başlığının arasından geçirilmesiyle ölçülür
Önemli noktalar
Optik eksen hizalaması ya da aralık ayarı, iş parçası yukarı veya aşağı sarkması olsa bile A+B’nin sabitlenmesini sağlamak için önemlidir.
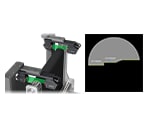
Rulo üzerinden kalınlık ölçümü (hedef hareket yönünde mevcut alan)
Uygulama örneği: Rulo pres işlemi sonrası kalınlık ölçümü
Algılayıcı kafaları, makara ve hedefin üst yüzeyleri alınan görüntü üzerinde tek bir düzlem olarak yansıtılacak şekilde yerleştirilir. Kalınlık, makaradan hedefin tepesine kadar olan adım ölçülerek bulunur.
Önemli noktalar
Hem şeffaf hem de opak hedeflerin kalınlık ölçümünü yapmak mümkündür. Hedeflerin kalınlığı makaraya bağlı olarak ölçüldüğünden, makara ile hedef arasında boşluk oluşmadığından emin olmak gerekmektedir.
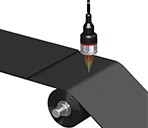
Rulo üzerinden kalınlık ölçümü (hedef hareket yönünde boşluk yoktur)
Uygulama örneği: Kauçuk levhaların kalınlık ölçümü
Kalınlık, hedef makaranın etrafına sarıldığında (yakın temas halinde tutulduğunda) makara yüzeyinin sıfır noktası olarak kabul edilmesiyle yükseklik farkı ile ölçülür.
Önemli noktalar
Hem şeffaf hem de opak hedeflerin kalınlık ölçümünü yapmak mümkündür. Hedeflerin kalınlığı makaraya göre ölçüldüğünden, makara ile hedef arasında boşluk oluşmadığından emin olmak gerekmektedir.
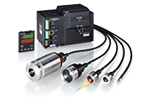
Kalınlık Ölçümü (çeşitli iş parçaları)
“Kalınlığı (çeşitli iş parçaları)” ölçmek için en uygun yöntemi ve en uygun ekipmanı bulabilmek için aşağıdaki örneklere bakınız.
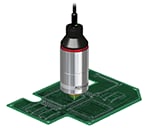
Şeffaf hedeflerin ölçümü
Uygulama örneği: Kaplama filmlerinin kalınlık ölçümü

Önemli noktalar
Yer değiştirme (deplasman) algılayıcılarının seçimi önemlidir
• Yer değiştirme (deplasman) algılayıcıları üst ve alt yüzeylerin her ikisini de görebilmek için yeterli aralığa sahip midir?
• Üst ve alt yüzeylerin yansıması farklı olsa bile düzgün ve tutarlı ölçüm gerçekleştirmenin mümkün olup olmadığını kontrol ediniz.
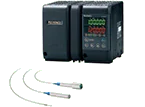
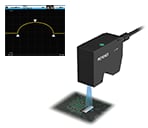
Referansa göre kullanılan yükseklik farklarına bağlı olarak opak hedeflerin ölçümü
Uygulama örneği: Sızdırmayan (su geçirmeyen) malzemelerin kalınlık ölçümlerinin yapılması
Kalınlık, 2D lazer yer değiştirme (deplasman) algılayıcısının kullanılmasıyla taban yüzeyi ve hedefin eş zamanlı olarak ölçülmesi, elde edilen profilden ölçüm adımı ile bulunur.
Önemli noktalar
Referans yüzey ve hedef arasında boşluk olduğunda hatalara meydana gelmektedir.
1. Yüzey plakası gibi yüksek hassasiyetli bir taban yüzeyi kullanılabilir.
2. Vakumlu temas veya manyetik temas kullanılabilir.
Yukarıdaki adımların uygulanmasıyla montajın iyileştirilmesi, ölçüm doğruluğunu önemli ölçüde artıracaktır.
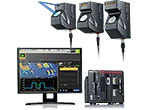
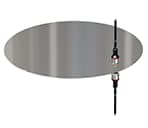
Üst ve alt yüzeyler arasındaki opak hedeflerin ölçümü
Uygulama örneği: Yonga plakalarının (Wafer) kalınlık ölçümü
Kalınlık, hedefin iki algılayıcı başlığının arasından geçirilmesiyle ölçülür.
Önemli Noktalar
• Deplasman sensörü hem üst hem de alt yüzeyleri görmek için yeterli menzile sahip mi?
• Üst ve alt yüzeylerin yansıması farklı olsa bile kararlı ölçümün mümkün olup olmadığını kontrol edin.
İki Sensör Kafası Arası Kalınlık Ölçümü Sırasında Alınması Gereken Önlemler
| Optik eksen hizalaması
Bir iş parçasının ölçümü iki sensör kafası arasında yapıldığında, iş parçası yukarı ve aşağı yönde titrese bile, prensipte ölçülen kalınlık değişmez.
Buna karşın, iki sensör kafasının optik eksenleri birbiriyle düz bir çizgide hizalanmazsa, iş parçasının yukarı ve aşağı titreşmesi veya bükülmesi nedeniyle ölçüm hataları ortaya çıkabilir. Dolayısıyla, aşağıda belirtilen noktalara dikkat etmek ve yerleştirmeyi optik eksenler hizalanacak şekilde yapmak oldukça önemlidir.
1) Optik eksenlerin yanlış hizalanmasının etkilerini azaltabilmek için, algılayıcı kafalarını silindirlere yakın yerleştirmek ve iş parçası geriliminin sabit, bir silindirden diğerine olan mesafenin ise küçük olduğu bir konum seçilmelidir.
Bu, küçük miktarlarda iş parçası bükülmesi ve titreşmesi durumlarında ölçümlerin yapılabilmesini sağlar.
2) Sensör kafalarını, şekilde gösterildiği gibi, yansıtılan ve alınan ışığın yönleri iş parçasının hareket yönüne dik olacak şekilde yönlendirmek gerekmektedir.
Bu da sensör kafalarının nakliye sırasında titreşimden dolayı iş parçasının hareket yönündeki eğilme ve sallanmalardan etkilenmesini engeller.
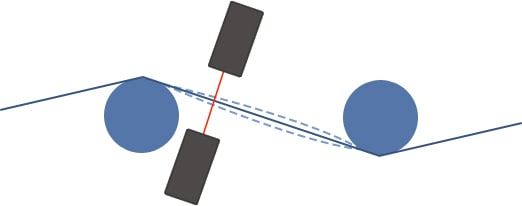
3) Optik eksen hizalaması sırasında, geçici ölçüm hedefi olarak ince beyaz bir reçine levhası veya bir kâğıt parçası ölçülebilir. Bu hedefler ölçüldüğünde lazer noktaları hedefin içinden geçer ve görülebilir hale gelir. Sensör kafaları, hedef yukarı-aşağı hareket ettirilse bile hedefin önündeki ve arkasındaki noktalar her zaman aynı hizada olacak şekilde takılmalıdır.
[Referans] Hedefin yukarı ve aşağı hareket ettirildiği durumlarda bile hedefin önündeki ve arkasındaki noktaların her zaman aynı hizada olup olmadığı kontrol edilmelidir.
Sensör kafalarını, hedefin yukarı ve aşağı hareket ettirildiği durumlarda bile lazer noktalarının merkezleri hizalanacak şekilde ayarlamak gerekmektedir.
Rulo Üzerinde Kalınlık Ölçümü Sırasında Alınacak Önlemler
| Rulo ve iş parçası arasındaki boşluk
Söz konusu makara referans alınarak bir iş parçasının kalınlığı silindir üzerinde ölçülürken, aralarında boşluk varsa ölçüm hataları meydana gelebilir. Dolayısıyla, aşağıda belirtilen noktalara dikkat etmek ve yerleştirmeyi boşluk kalmayacak şekilde yapmak oldukça önemlidir.
1) İş parçasına mümkün olduğunca fazla gerilim uygulanmalıdır. Gerilim zayıfsa, iş parçası makarayla tam temas etmeyecektir. Bu nedenle, birkaç mikrometreden onlarca mikrometreye kadar değişen bir boşluk oluşacaktır. İş parçasının gerilme kuvvetini göz önünde bulundurarak 50 N veya daha fazla gerilim uygulanan ölçümler yapılması önerilir.
Ölçümler, iş parçası geriliminin mümkün olduğunca sabit olduğu, bir silindirden diğerine olan mesafenin az olduğu ve iş parçasının silindirin üzerine yerleştirildiği bir konum üzerinden gerçekleştirilmelidir.
2) Optik eksen, silindirin tepe konumuyla hizalanmalıdır.
Şekilde gösterildiği gibi, optik eksen silindirin tepe konumuna uygun hizalanmazsa, ölçüm hatası (Z aralığı) oluşur.
a) Besleme yönünde algılayıcı kafası konumunun ince ayarlarını yapabilen bir mekanizma yerleştirilmelidir.
b) Optik eksen, makaranın tepe konumuna uygun hizalanmamış olsa bile, Z boşluğunu en aza indirebilmek amacıyla büyük çaplı bir silindir üzerinde ölçüm yapılabilir.
Yukarıda listelenenler gibi değişiklikler yapmak gerekmektedir.
| Silindir eksantrikliği (eksantrikliği)Dış merkezlilik
Silindir döndüğünde, silindir dış merkezli olduğundan dolayı ölçüm hataları meydana gelebilir.
Silindirin dış merkezli oluşunun getirdiği etkileri ortadan kaldırabilmek için aşağıda belirtilen noktalara dikkat edilmelidir.
1) Kalınlığı ölçmek için kullanılan konumlar iş parçasının her iki kenarı olduğunda, adım değeri üzerinden kalınlığı bulabilmek için hem silindir yüzeyi hem de iş parçası yüzeyi aynı anda ölçülmelidir.
2) Silindirin referans olduğu bir makara üzerindeki iş parçasını ölçerken, silindir dış merkezli olarak hareket etse bile bu durumun etkisini ortadan kaldırabilmek için ölçümler aynı dönüş açısında (konumda) gerçekleştirilmelidir.
İdeal ölçüm sistemini seçebilmek için bilinmesi gereken ölçüm ve ipuçları hakkında her şeyi içeren ve mutlaka okunması gereken bir kılavuz!
Bu kılavuzda, ölçüm sistemlerinin tanıtılmasının yanı sıra kalınlık, dış çaplar, şekil ve daha fazlasını ölçmek için kullanılabilecek en iyi yöntemler ayrıntılarıyla anlatılmıştı.